From Foundation to Future: The Environmental Impact of ICF Construction
From Foundation to Future: The ENvironmental Impact of ICF Construction
As sustainable construction moves from niche to necessity, the materials and methods we build with are facing increased scrutiny. Among the alternatives gaining attention, Insulated Concrete Forms (ICFs) stand out for their blend of structural strength and energy performance. But to truly understand their environmental impact, it’s important to look beyond surface-level benefits and examine the full lifecycle—starting with how ICFs are made, how they’re used on-site, and how they perform over decades of occupancy.
manufacturing icfs: a balanced beginning
ICFs are made from rigid foam—typically expanded polystyrene (EPS)—formed into hollow, interlocking blocks that stay in place after concrete is poured. EPS is derived from petroleum and manufactured using heat and steam, giving it an energy-intensive but highly efficient production process.
Many ICF manufacturers, including Nudura, use virgin EPS. This ensures consistent density, structural integrity, and thermal performance. While virgin EPS isn’t recycled content, it is lightweight, inert, and dimensionally stable, offering long-term environmental benefits through energy conservation and durability.
Compared to other construction inputs:
- Wood framing uses renewable materials but often contributes to deforestation and requires chemical treatments to prevent rot or infestation.
- Concrete masonry units (CMUs) use similar cement-based materials as ICFs but require more raw materials by volume and often additional insulation to meet energy codes.
Summary: While EPS is petroleum-based, its role in ICFs is minimal by weight and contributes significantly to the overall performance and durability of the structure.
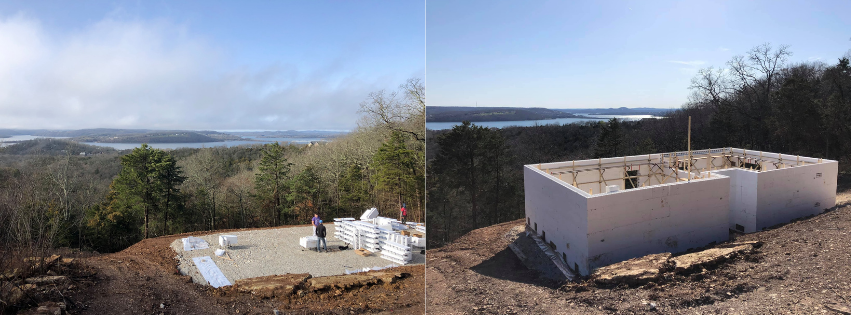
No mess, no waste, just results. From block delivery to pour day, ICF construction delivers clean builds with lasting performance.
job site efficiency: construction with less waste
ICFs offer multiple environmental advantages during construction. The forms are modular and easy to cut, producing minimal waste—much of which can be reused on-site. Due to the double-layer of continuous foam insulation built into the forms themselves, there's no need for separate insulation crews.
By comparison:
- Wood framing generates substantial scrap and packaging waste.
- CMU projects often involve mortar waste, chipped blocks, and more frequent material deliveries.
ICFs also reduce emissions from job-site equipment due to faster build times and fewer deliveries. Their lightweight nature also minimizes transportation impact compared to heavier materials like CMUs.
Summary: Faster assembly, less labor, and significantly reduced waste make ICFs a cleaner, more efficient construction method than traditional alternatives.
operational impact: energy efficiency and comfort
The environmental payoff of ICFs grows over the building’s lifetime. ICF walls consist of two layers of continuous insulation surrounding a solid concrete core. This creates a thermal envelope that offers R-values of R-23 or more, with exceptional airtightness. Once the reinforced concrete core is cured, the energy efficiency increases to a performance value of R-50, one of the highest R-values possible.
Compared to:
- Wood-framed walls, which are prone to thermal bridging and air infiltration. The standard R-value for stud-framed walls is R-13 with a range up to R-20 (with advanced framing techniques and additional insulation).
- CMU walls, which have minimal inherent insulation. The blocks themselves only have an R-value of 1.99, relying entirely on added insulating materials to meet code.
ICFs also leverage thermal mass. The concrete core absorbs and stores heat, reducing interior temperature swings and decreasing HVAC system demand.
Real-world performance studies have shown ICF buildings can use 30–70% less energy for heating and cooling, dramatically reducing operational carbon emissions over time.
Summary: High insulation, airtightness, and thermal mass make ICF walls one of the most energy-efficient systems available.
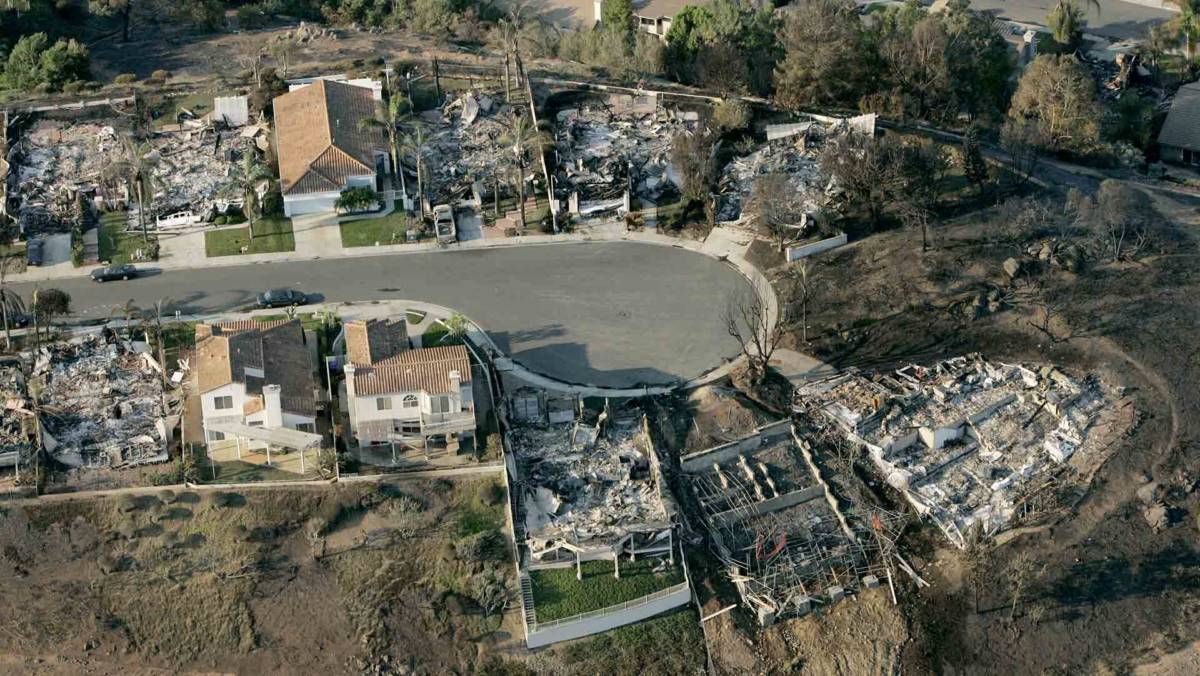
Three ICF homes remain standing after a wildfire in a suburb of San Diego, CA.
durability and disaster resilience: fewer repairs, less waste
ICF buildings are built to last. The combination of reinforced concrete and EPS foam is highly resistant to rot, moisture, mold, pests, and natural disasters. ICF walls routinely meet or exceed fire ratings up to 4 hours and are designed to withstand wind loads of 250 mph.
In contrast:
- Wood structures have a shorter service life and often require repairs due to environmental wear or insect damage.
- CMUs, while strong, are prone to cracking and can require frequent maintenance or waterproofing.
The longer service life of ICF buildings means fewer repairs, less maintenance, and lower material consumption over time—all critical factors in a building’s environmental footprint.
Summary: ICF’s resilience and durability reduce lifecycle environmental impact by minimizing material use and repair frequency.
embodied vs. operational carbon
A frequent question about ICF construction concerns embodied carbon—especially from concrete and EPS. It’s true that these materials require more energy to produce than wood, but they also last longer and perform better.
- Cement production contributes to global CO₂ emissions, but low-carbon concrete mixes are increasingly available and help reduce this footprint.
- EPS foam does not off-gas harmful substances, and its insulation performance results in major operational carbon savings.
Most ICF buildings offset their embodied carbon within 5–10 years through reduced energy use. Over the full building lifespan, ICF systems typically outperform wood and CMU in net carbon impact.
Summary: While ICFs carry more embodied carbon up front, the operational savings and longevity offer a clear long-term environmental advantage.
eps foam and recycling: innovation ahead
Recycling EPS foam has traditionally been limited, largely due to collection challenges and its lightweight structure. However, innovations are emerging. One notable example comes from Hawaii, where post-consumer EPS—such as foam surfboards—is being recycled into insulated composite concrete forms (ICCFs).
While this process is not yet widespread, it demonstrates the potential for future recycling streams and circular reuse of EPS in structural applications. The recyclability of concrete also supports material recovery at end-of-life.
In contrast:
- Wood waste is often treated with chemicals and may be landfilled.
- CMU waste is heavy and rarely recycled, often ending up as demolition debris.
Summary: Though currently uncommon, EPS recycling innovations are growing. ICF systems remain inert and stable at end-of-life and can be partially reclaimed depending on local infrastructure.
conclusion: a high-performance, low-impact solution
When viewed across the full lifecycle, ICF construction offers one of the most sustainable and high-performing solutions in the industry. Its combination of efficient manufacturing, low-waste installation, superior energy performance, and long-term durability significantly reduces a building’s environmental burden over time.
Compared to wood framing and CMUs:
- ICFs produce less waste and require fewer materials.
- They deliver better energy efficiency with lower emissions.
- They outlast traditional systems, reducing the need for replacement.
- As recycling innovations expand, the environmental case only strengthens.
For builders, developers, and homeowners aiming to reduce their environmental footprint without compromising performance, ICFs represent a smart, future-ready path forward.
Ready to Build Smarter?
At ICF Walls of the Ozarks, we believe sustainability should start with the foundation. Whether you're planning a custom home or evaluating energy-efficient construction options, our team is here to help you explore the long-term benefits of ICF. Reach out today to start your journey toward a stronger, more sustainable, and energy-efficient home.